Atomising Nozzles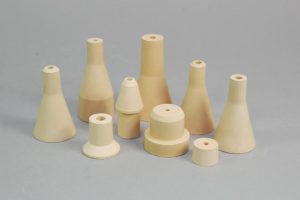
Powder metallurgy is a cost effective process despite the convoluted manufacturing route of deconstructing the starting material, utilising the atomisation process, and then reconstructing the product in separate forming and heating stages. And then, there are the immiscible mixes with unique properties that couldn’t be made any other way.
It is the atomisation process that is of interest to us. Nozzles controlling the flow of molten metal from the crucible whilst being bombarded with a high pressure jet of air, inert gas or water.
A principle feature of all the nozzles is their close dimensional accuracy, which promotes stable flow characteristics under the most arduous conditions.
For best erosion resistance, the yttria stabilised Zirconia OZA is the product of choice with superalloys.
Zirconia MCA is stabilised with a mix of ceria and magnesia, and exhibits excellent thermal shock resistance.
Zircon nozzles are used for the atomisation of iron and aluminium.
Finally, composite nozzles, where an alumina outer body is pressed onto the nozzle, allows the use of ultra-high density nozzles with the capability of markedly increasing the campaign/sequence time.